View of Iron Production
Science 14th century furnaces were developed that could not only produce iron but at the same time,the melted iron ore called pig iron. In 1982 about 98 % of Iron was produced via Blast furnace. About 1945 the direct reduction process was developed and from about 1970 the industrial production was started. This process is very suitable for countries with low cost natural gas. Smelting-Reduction Processes were started to develop about 1970 and is therefore quite new with a great potential for the future
Blast furnace
The iron ore is typically smelted in Blast furnaces that use primarily iron ore, iron concentrate pellets, metallurgical coke, limestone and lime as the row materials.The iron produced from the blast furnace under these conditions, is relatively expensive as compared to current alternative direct iron reduction process. The product of this process is called pig iron (Fig1)
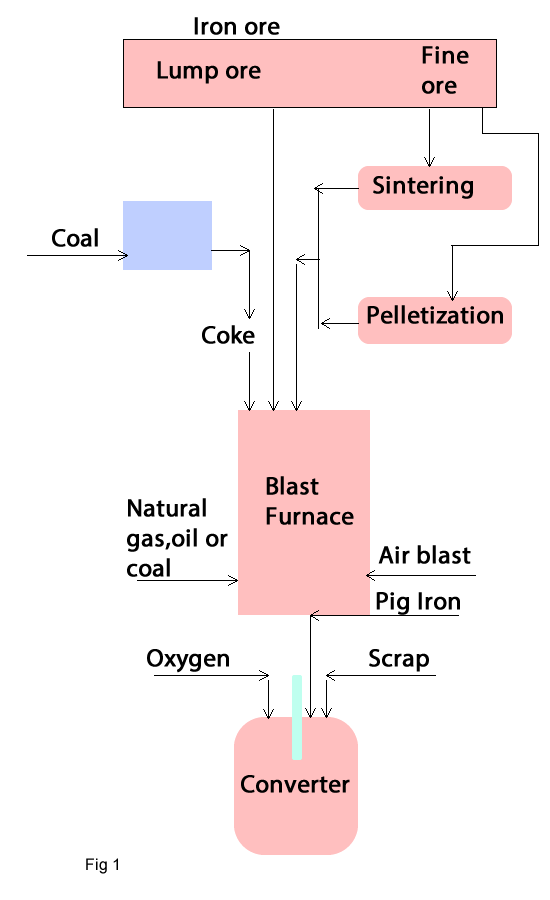
Direct reduction process
Direct reduction process is when fine (pelletized) or lump ore are reduced in solid state at the relatively low temperature of about 900 -1100 oC using reformed natural gas. The product is called sponge iron (Fig2)
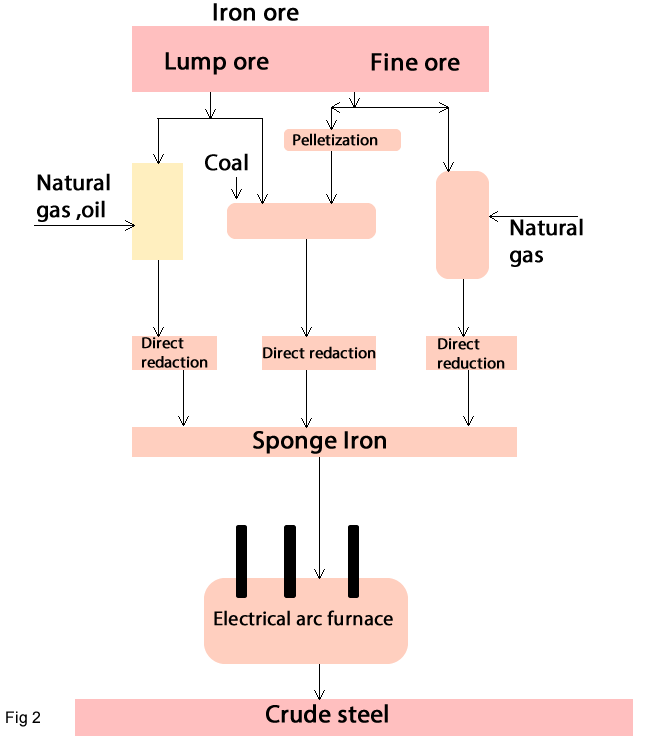
Smelting-Reduction Processes
Around 1970s,the smelting-reduction process started. This process is relatively new; however it seems that it may be the way of future. In this process the ore is pre-reduced with gas and then melted in vessel, where melting energy is produced by oxidation of coal. Some process use also electrical energy in the melting stage (Fig3)
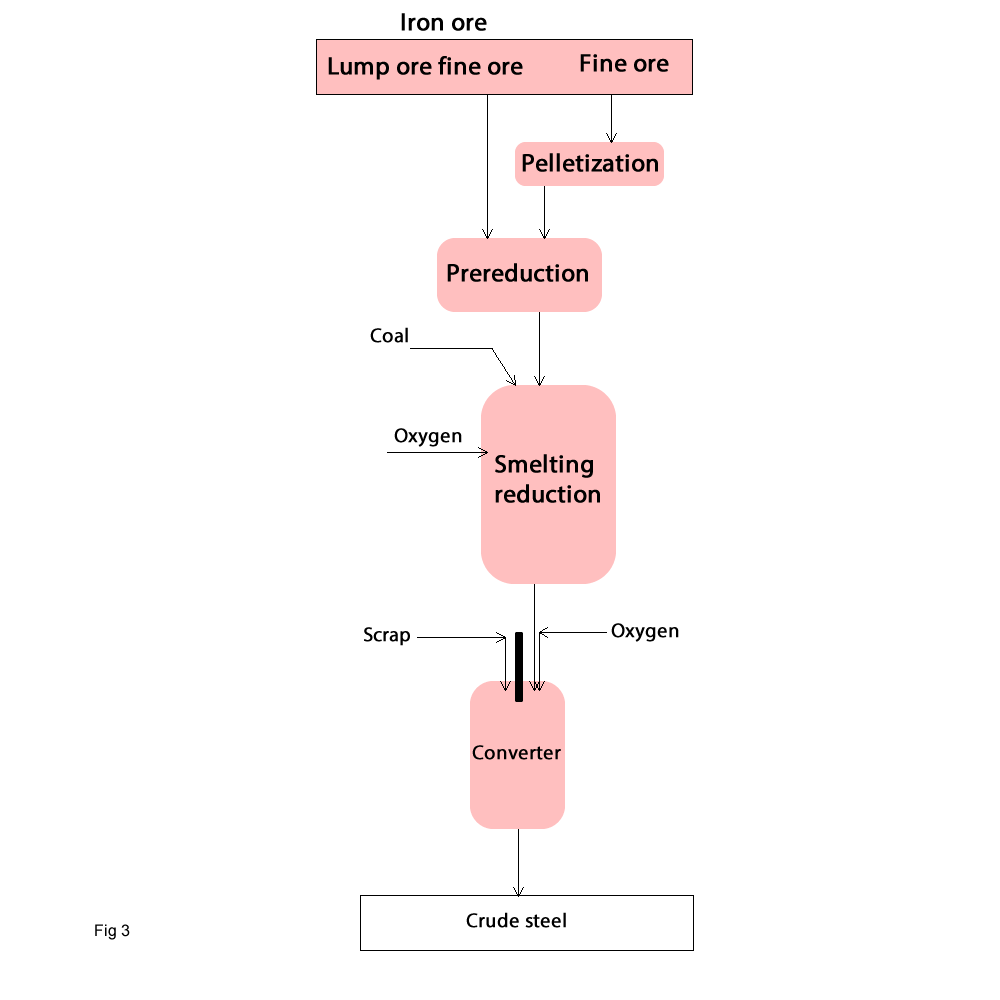
Steelmaking
Steel production depends on the availability of raw materials such as pig iron, scrap and sponge iron. There are two fundamentally different methods (Fig. 1, 2 and 3):
- Converter process: blowing oxygen into liquid iron (pig iron).
- Electrical Arc Furnace: smelting iron containing materials, such as scrap and sponge iron